The fruits of innovation
title
The fruits of innovationshort_title
author_rel
author
is_scheduled
Nopublish_date
summary
Investments made by the company and the National Development Contract enabled technological innovation, efficient processes, and sustainability to flourish at the Pomigliano plant.
text
The research and development of new technologies, as well as the consolidation and upgrading of production capacity at the Pomigliano d'Arco plant (Naples), are some of the key investments started by the company in 2019 – through the 505 Development Contract* signed with the then Ministry of Economic Development and Invitalia – which demonstrate their effectiveness today.
Investment totaled about €61 million over a period of five years. Out of this total, €18 million came as a contribution from the state for industrial investment (about €12 million) and for investment expenditure in R&D (about €6 million).
A broad, complex project with six different implementation objectives (IOs) aimed at innovating technologies and improving production processes, as well as consolidating the Campania plant’s position among the international benchmarks for the production and testing of aeronautical components and engines.
At the same time, the goal of research and development activities has been to acquire strategic know-how in various areas: from technologies applicable to combustors to machining operations via the technologies needed to optimize turbine component production and maintenance capabilities.
"With our research activities in recent years, we have been able to develop new skills and capabilities, designing innovative components that contribute to reducing the emissions and fuel burn of aircraft engines," explains Carlo Silvestro, Engineering Manager at Avio Aero. The work of engineers in Pomigliano d’Arco has also made it possible to "implement solutions to optimize the cooling efficiency of the components, which extends their operating life and improves reliability."
The results achieved in the six implementation objectives have helped contribute to developing technologies to reduce the environmental impact of air transport, increase the plant’s production capacity, and equip the company with unique skillsets in Italy and – in several cases – Europe.
This is the case with the innovative shaped cooling holes technology used – in GE Aerospace – in Pomigliano and only one other plant (in Indiana). Still, more importantly, it allows microperforations to be created in the walls of the combustion chamber of aircraft engines to protect the materials it is made up of.
This capability was developed entirely in-house at Pomigliano. It offers a major competitive advantage: this technology could be applied in next-generation engines powered by both traditional fuels and hydrogen, increasing the operating life of the combustion chamber materials and, consequently, of the whole component.
"Research was carried out in collaboration with Federico II University and Unicampania, with students and researchers providing technological and statistical support in the development of the technology, regarding the use of the laser and innovative verification methods," says Gaetano De Chiara, CME of Avio Aero.
That’s not all – other uses of laser technology are being explored in Pomigliano: one of the most promising involves replacing traditional sandblasting with more advanced laser texturing to increase the performance of the ceramic protections of the materials the combustion chamber is made of and reduce its environmental impact.
"To date, we have just one test before proposing this solution to the GE Aerospace Design Board. So far, we have demonstrated that it is possible to use lasers to create a base for spraying ceramic protective coatings on materials", De Chiara continues. "Once testing is completed, our plant will offer the aviation sector a unique capability to reduce production costs and environmental impact."
Alongside combustor applications, the Development Contract also included the technological development of new capabilities for the Pomigliano plant, including constructing the exhaust and mixing duct (Turbine Exhaust Case and Mixer) for a state-of-the-art turbofan engine. A multi-faceted project with an innovative approach and concept: the ingenuity of the engineers working on this goal led to using additive manufacturing – or 3D printing, specifically with Direct Metal Laser Melting technology – to make some components.
Other veins of research included a special test carried out on a turbofan engine, which was completed in 2019 and contributed to increasing the plant’s engine testing capacity, but also the optimization of technologies for producing and maintaining low-pressure turbine nozzles. In fact, one of the main goals set by Avio Aero is to optimize production cycles to increase productivity while reducing costs and processing times and extending the operating life of the components. All these goals have been achieved.
As for increasing production skills, major strides have been made in High-Speed Milling – thanks to investments since 2019 – and in the ‘masking’ process for turbine blade repair. Both processes can be applied to titanium aluminide (TiAl) blades produced by additive manufacturing in the Cameri plant. The High-Speed Milling process was developed to quickly remove excess waste material, reducing processing times and milling capacity.
Research efforts to improve the masking process and plasma spraying operations have resulted in major improvements, moving from using silicone to creating a metal mask. This has saved time and reduced the process’s cost and environmental impact.
These technical and process achievements make Pomigliano d’Arco a matter of pride for the company, where its unique skills and capabilities range from the engineering teams’ work to applications in production, including testing and maintenance of aircraft components and engines
*CDS_000505 (CUP no.C53D16000770004 Industrial research and experimental development project funded under the PAC ‘Action and Cohesion Plan - Third and Final Rescheduling’)
category
landing_landscape_hero
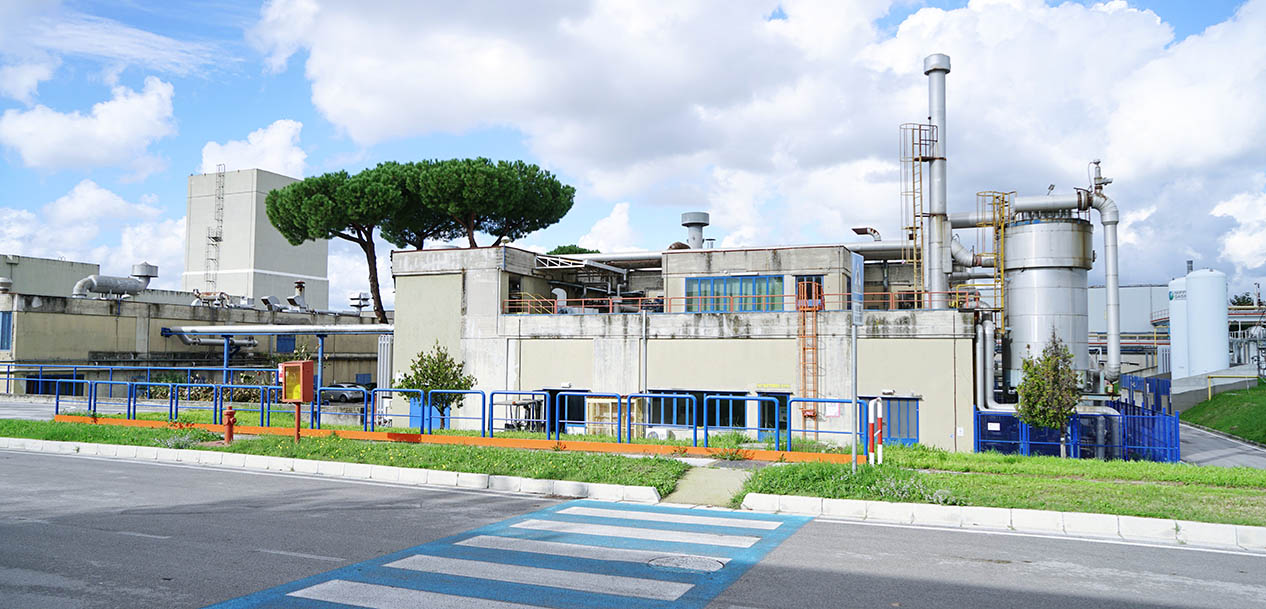
image_hero_mobile_web
image_hero_mobile
image_square
video
video_article_is_published
Novideo_slider_is_published
Nods_summary
Nello stabilimento di Pomigliano, gli investimenti dell’azienda e il Contratto di Sviluppo nazionale fanno fiorire innovazione tecnologica, processi efficienti e sostenibilità.
metadata
Title:
Description:
Keywords:
Use in sitemap: No
Change frequency: always
Priority: 0