Introducing FLIGHT DECK
title
Introducing FLIGHT DECKshort_title
author_rel
author
is_scheduled
Nopublish_date
summary
The GE Aerospace lean operating model reinforces the approach adopted across Avio Aero's teams aiming at continuously improving and making the way of working agile and sustainable.
text
The steady and sustained growth of air transport in recent years, with the pandemic slowdown in between, might seem to be the main reason why GE Aerospace has long been promoting Lean and a culture of continuous improvement around the world. Lean has been well known for at least thirty years in other industrial sectors – starting from the automotive one, where Toyota was the pioneer.
Having made significant progress implementing lean, GE Aerospace’s operating model FLIGHT DECK is the natural next step in the companies’ transformation: this systematic approach is helping run the business to deliver exceptional value as measured through the eyes of the customers. Though, the main reason is - first and foremost - safety, that must be guaranteed together with quality, essential prerequisites for the aviation industry.
This system is how we, at GE Aerospace and Avio Aero, are running the company, and it is helping us bridge strategy and results. It is applicable to everyone – literally, at every level, from the CEO to the top management to the engineers and workers and is highly impactful.
The implementation of this system also involves familiarizing and activating a glossary of evident Japanese derivation: Kaizen, Shingijutsu, Hoshin Kanri, Genba... All words that are becoming increasingly familiar among employees and (between the enthusiasm for novelties that mixes with the natural skepticism of human environments) find a place in the daily routine thanks to teams of experts who facilitate understanding and adoption.
"FLIGHT DECK is a simplified and organized model that collect all these Lean principles and tools," explains Fabiana Panni, Lean & Business Operations Leader. "This is what we have been doing for years now, which we have come to know, organized in a working model with 10 Fundamentals that capture the spirit of Lean and on which we must persevere precisely because it is only with this exercise that continuous improvement takes place."
"We do not adopt Lean for ourselves, or for an exercise in corporate virtuosity, but to bring value to the customer: and this value is clearly found in the acronym SQDC – Safety, Quality Delivery Cost," says Panni. "If a company creates safe products, which do not present quality problems, if it delivers them on time and at a competitive cost, it generates value for both its customers and its shareholders, but above all for its people".
The 10 Fundamentals of FLIGHT DECK, mentioned by Panni, are the basis of this value generation. They are equally divided into two groups of 5, starting from the Fundamentals of the individual: continuous improvement (Kaizen), Respect for People, Problem Solving, Action planning and customer-driven.
And 5 other Fundamentals are based on the enterprise: standard work, daily & visual management, value stream management, operating cadences and the translation of the strategy in execution (Hoshin Kanri).
"We do not adopt Lean for ourselves, or for an exercise in corporate virtuosity, but to bring value to the customer: and this value is clearly found in the acronym SQDC – Safety, Quality Delivery Cost"
"The fundamentals are nothing new for Avio Aero," says Panni. "In a nutshell, we need to have a strategy that guides us (Hoshin Kanri) and a standard of work that allows us to generate the results we collect on a day-to-day basis, obviously related to SQDC; so, thanks to the operational cadence, we can get a complete view of the trend both on a daily basis and with respect to the overall strategy."
Tools and methods that cannot work without the dedication and skills of people: aiming for continuous improvement, always with those who allow you to work in mind, i.e. Customers (whether they are internal or external to the company) and respect for People, are the key to succeeding in all this.
"Problems are the bread and butter of our days," adds Panni about Problem Solving, also debunking a cliché that accompanies work standards. "There is no problem that cannot be addressed through in-depth analysis (where and why) to find the real root cause and define a plan to solve it. Often, standardization is seen as flattening, but I prefer to see it as the force of transformation: using standards shared by all, we apply creativity to look for the problem and solve it with greater focus, using a common language. Neglecting this has sometimes not allowed us to make progress in solving problems."
The fundamentals of FLIGHT DECK have been applied for some time at Avio Aero. For example, during events that introduce and extend such practices in its sites across Italy, the Czech Republic and Poland. Just a few days ago, the team at Rivalta di Torino plant dedicated a week to Shingijutsu, with the guidance of a Sensei who accompanied a large group of workers, engineers, employees and leaders from various locations around the world and different departments in a work of research into production improvements and efficiency.
Recent cases of the FLIGHT DECK in action can be found in the improvement of management and delivery for engine programs such as the LEAP ("best seller" engine for which Avio Aero produces several components) and for the maintenance services of the EJ200 engine for the Eurofighter Typhoon. But they are also found in projects dedicated to the energy efficiency of entire plants, part of the climate neutrality commitment pursued by GE Aerospace and Avio Aero. As Angelo Carlucci, Global Supply Chain Lean and Development Leader, explained.
"Recently, at the Avio Aero plants in Bielsko Biala (Poland) and Pomigliano d'Arco (Italy), our cross-functional teams have worked to find the causes and test alternative, innovative methods, and have implemented solutions aimed at reducing the energy consumption of production machinery or supply systems that have allowed us to reduce consumption by hundreds of MWh and costs by hundreds of thousands of dollars," says Carlucci.
"We work as a single team, with a single model," Panni concludes, quoting her favorite Lean theorem. "This allows us to think of ourselves as a single company that operates in a uniform and shared way, and to go to the heart of the problem by addressing it from different points of view. The projects that work best are those where each department contributes its own culture, knowledge and 'fresh eyes'. For me, working together with a single goal and model is the only way to overcome the complex problems that modernity poses, aiming at higher challenges. An effective and efficient way... And even more enjoyable!"
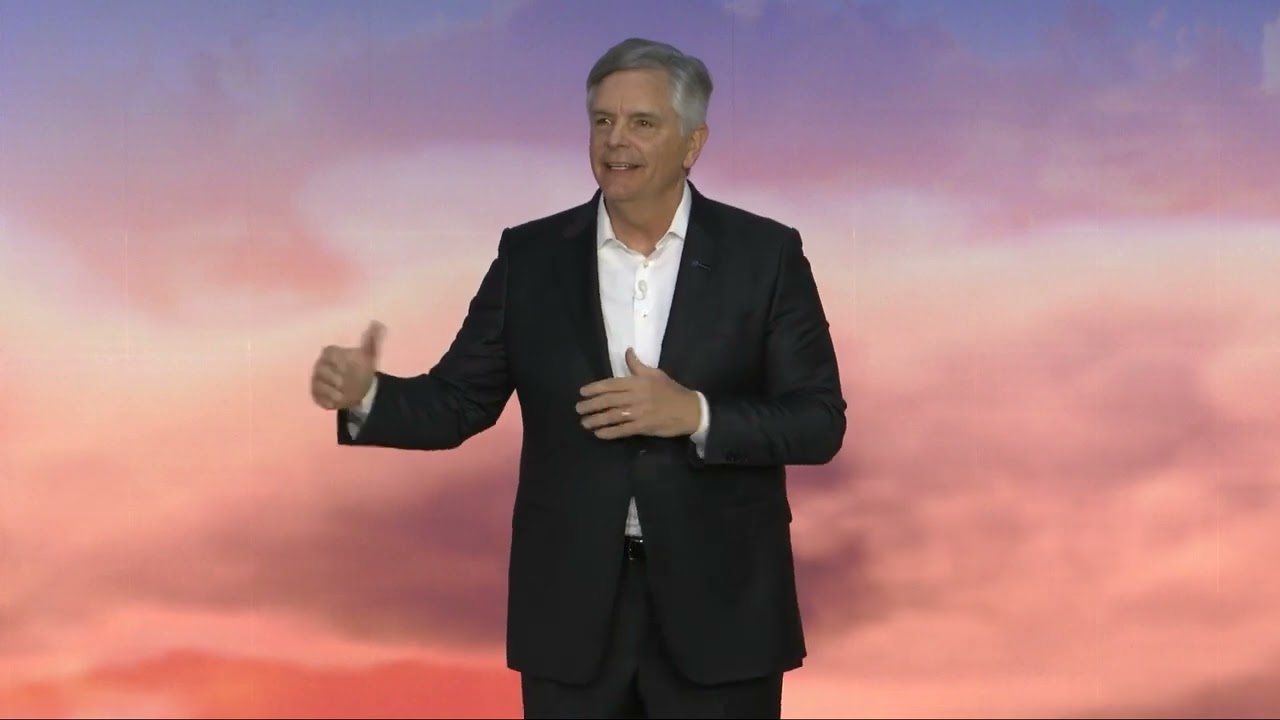
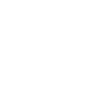
category
landing_landscape_hero
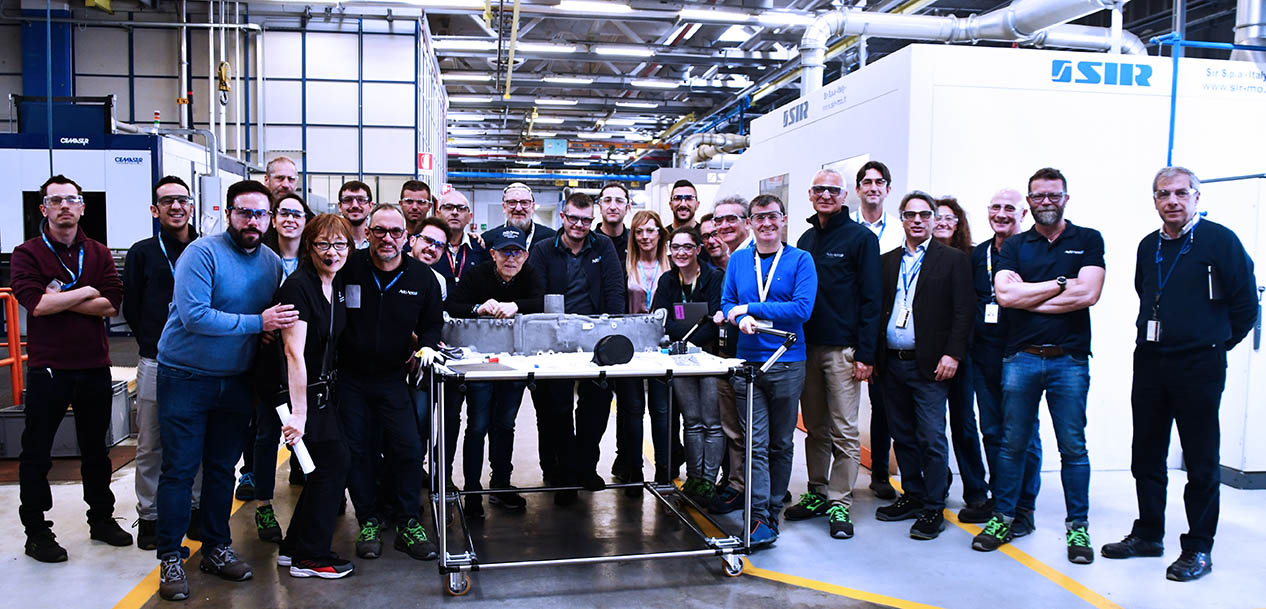
image_hero_mobile_web
image_hero_mobile
image_square
video
video_article_is_published
Novideo_slider_is_published
Nods_summary
The GE Aerospace lean operating model reinforces the approach adopted across Avio Aero's teams aiming at continuously improving and making the way of working agile and sustainable.
metadata
Title:
Description:
Keywords:
Use in sitemap: No
Change frequency: always
Priority: 0