High performance, utmost Safety
title
High performance, utmost Safetyshort_title
author_rel
author
Marinella Marconiis_scheduled
Nopublish_date
summary
The RACER demonstrator continues its flight campaign equipped with advanced transmissions and cutting-edge materials, capable of passing extreme tests.
text
In the midst of the crowd of experts, employees, reporters and priviliged guests of Airbus Helicopters that gathered at the aircraft test center in Marignane - a few kilometers from Marseille in France - on last May 15 to admire the RACER in flight, there were also Lorenzo Dal Mas and Arcangelo Barletta. They were part of the group invited from Avio Aero, partner in the program for the main rotor and side rotor transmission systems.
The RACER program* has had a special relevance for Avio Aero since its inception in 2015, when it was still in the form of technical drawings and CAD. Today, the Airbus Helicopters team is leading a flight campaign that will allow them to explore the so-called "flight domain" and, therefore, to validate all the features and performance for which this futuristic helicopter was conceived. First of all, high speed with reduced carbon and noise emissions.
Dal Mas and Barletta are actually part of a broad team of about 90 people from different company functions, based between the Avio Aero sites in Rivalta di Torino, Borgaretto, Torino-Sangone and Bielsko Biala. Between these locations, the components of the RACER for which Avio Aero is responsible have been developed and built: the central transmission (or main gearbox, MGB) and the two lateral gearboxes (LGB) that move the propellers placed on the wings with an innovative design (called box wings).
Transmissions play a central role, providing the power needed for operation and flight, maximizing efficiency and ensuring high levels of reliability. For this reason, the tests (in all simulated flight conditions) to which they are subjected are extremely hard and intense. This is explained by Del Mas, CTH Senior Engineer, who joined Avio Aero in 2014 after a doctorate in Industrial Engineering, within the Edison program to deal with support to in-service programs.
"Thanks to the Edison program, I got introduced to the world of transmissions (at first, commercial engines from GE Aerospace and other manufacturers) and became passionate about their design. In the various projects, I was able to study the fatigue properties for gear materials and over time I approached the world of helicopter transmissions. Finally, right with the LGB module of the RACER. In the following years, I took on a role more dedicated to module design, and then made RACER my main activity in my working group for a long time," says Del Mas, who in the meantime is working on other helicopter products and on the transmissions of the AMBER demonstrator, part of Clean Aviation.
The partnership with his colleague Barletta, Mechanical Transmission Component Design Engineer at Avio Aero since December 2015, was born precisely at the beginning of the transmissions’ concept design phase for the RACER and was "cemented" (it is appropriate to say) in the following years, as he himself explains: "I specialized in bearings and shafts, working on the RACER modules and other helicopter designs, going through the various stages of transmission development, from design to component validation and testing." The latter activity culminated in the passing of one of the most arduous tests, the oil-off.
"Our innovation lies in the inclusion of new materials and new technologies, with all the difficulties and excitement for an engineer that this brings"
The oil-off test is a bench test required by international regulations governing flight safety and which verifies that each component of the transmission retains its operational capabilities even in the (very unlikely) event of total oil loss, thus ensuring that the aircraft is still capable of landing safely.
"The LGB specification of the RACER had two types of requirements for oil-off operation," Dal Mas explains. "A first mandatory requirement to obtain a flight permit (minimum requirement for a demonstrator) and a second, strategic, definitely more challenging and more with a view to product optimization for future helicopter applications. In fact, demonstrating that a transmission can work without lubrication offers many advantages: in the event of malfunctions, very long missions can be completed (think for example of flights on off-shore platforms where most of the time is spent in the open sea, or rescue operations), reducing the severity of the event".
Right from the start, the Avio Aero team decided to work on a design that would allow them to achieve the most complex requirement, the strategic one, and took up the challenge by trying to introduce both innovative design solutions and new materials that had higher performance than those traditionally used, especially in conditions of absence of lubrication.
"The lateral gearbox consist of two bevel gears, a shaft that transmits power to the side propeller, and an accessory gear that draws power to power the oil pump. The rotation speed of the rotor is less than 2000 rpm. Our innovation lies in the inclusion of new materials (such as M50Nil, a special alloy resistant to stress and high temperatures) and new technologies (ceramic bearings, heat exchangers in additive manufacturing), with all the difficulties (and excitement for an engineer) that this brings", continues Dal Mas.
The list of innovations is confirmed, and integrated, by Barletta, which highlights how these are a founding element of the RACER project. "The main CTQs (critical elements for quality) that guided our choices were weight and performance in lubrication loss conditions. Innovations such as additive, or metal 3D printing, have made it possible to integrate into the heat exchanger (an internal component of the transmission, ed.) additional functions, to reduce the number of its components, their dimensions and therefore their weight. The rotating parts, above all gears and bearings, represent the most critical component of the transmission, and the use of innovative materials and hybrid bearings has allowed further reductions in overall dimensions and, ultimately, the passing of the oil-off test".
The concentration of innovation together with the unprecedented experience of creating and testing products with unique characteristics, in extreme conditions, has generated a series of memorable emotions for the engineering teams. "The test campaign was experienced by everyone with a lot of curiosity, emotion but also tension," says Dal Mas.
The two engineers meticulously retrace every phase of the tests that they have passionately followed from the beginning, inside the control rooms of Avio Aero's Sangone experimental center. Each test provides a large amount of data that is recorded and analyzed with the rest of the team. "The first oil-off test was done on the left LGB and it was limited to a duration of about 40 minutes. Arcangelo and I were sitting close together in the room monitoring the temperature trend moment by moment, which we knew was one of the most significant parameters to keep under control," says Dal Mas.
After this heart-pounding first, the temperature values were reduced and then stabilized so as to complete the test with a lot of applause, also legitimized by a careful inspection carried out downstream of the test which found that the individual parts of the transmission (gears, teeth, bearings) were in optimal condition. "These tests were a unique emotional swing, given the fine balance that governs the evolution of the test and its final outcome. I believe that from tests like these, the world of power gearboxes can draw the most ideas. The parts were in excellent condition, so much so that they did not stand out from what had been tested in the presence of lubrication," says Barletta.
On the strength of this first result, the team "raised the bar" and also tested the second lateral transmission, the right one, pushing it beyond four hours of operation without lubricant. "We wanted to learn as much as possible and verify the customer's strategic requirement," Dal Mas continues. "In this case, we were still pushing ourselves beyond anything we'd ever done. Minute after minute, hour after hour, we reached and even exceeded the goals we had set for ourselves: at the end of the test we burst into another liberating applause! We are all aware that oil-off performance is strongly linked to specific system features and boundary conditions, therefore the obtained results are valid for this specific gearbox. Such positive evidence from these tests are relevant for future projects.”
However, both Dal Mas and Barletta are certain that this is just the beginning. "I consider myself a more than lucky engineer. Contributing to the project starting from a blank sheet of paper, with a continuous, deep collaboration with the customer, was a unique experience. Now, a new great opportunity for growth awaits us: to support the flight phase of the RACER and respond 'present' to the new challenges, also involving and supporting the younger members of the team" concludes Barletta.
RACER images in page are courtesy of Airbus Helicopter.
*This project has received funding from the Clean Sky 2 Joint Undertaking (JU) under grant agreement No 945542. The JU receives support from the European Union’s Horizon 2020 research and innovation programme and the Clean Sky 2 JU members other than the Union.
category
landing_landscape_hero
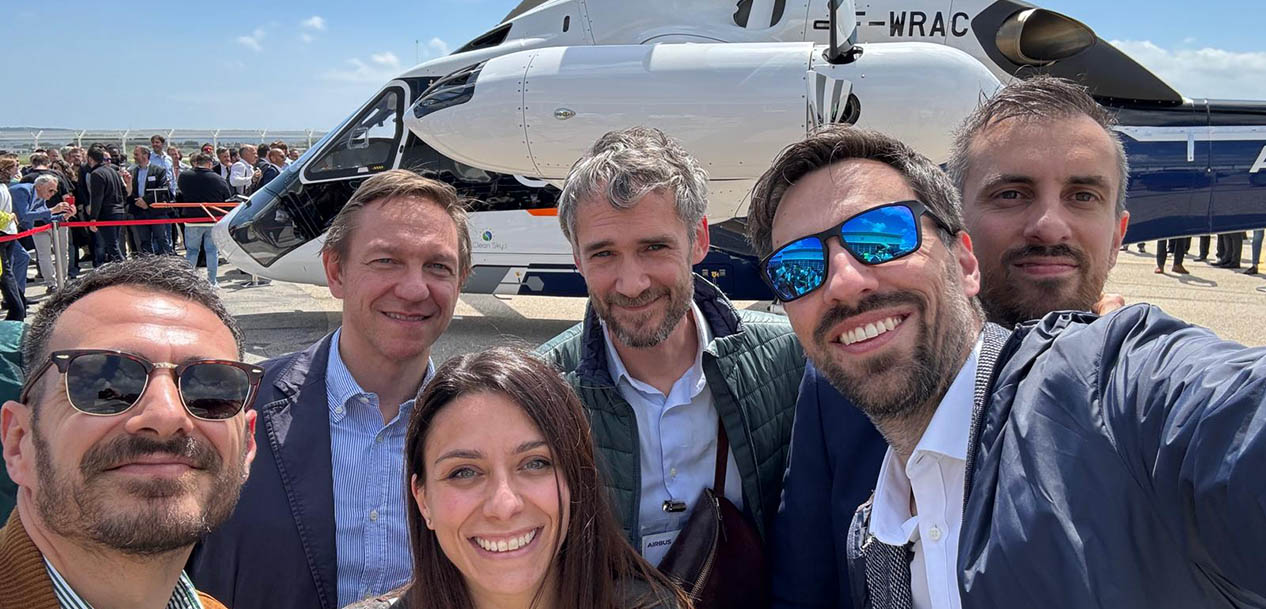
image_hero_mobile_web
image_hero_mobile
image_square
video
video_article_is_published
Novideo_slider_is_published
Nods_summary
The RACER demonstrator continues its flight campaign equipped with advanced transmissions and cutting-edge materials, capable of passing extreme tests.
metadata
Title:
Description:
Keywords:
Use in sitemap: No
Change frequency: always
Priority: 0